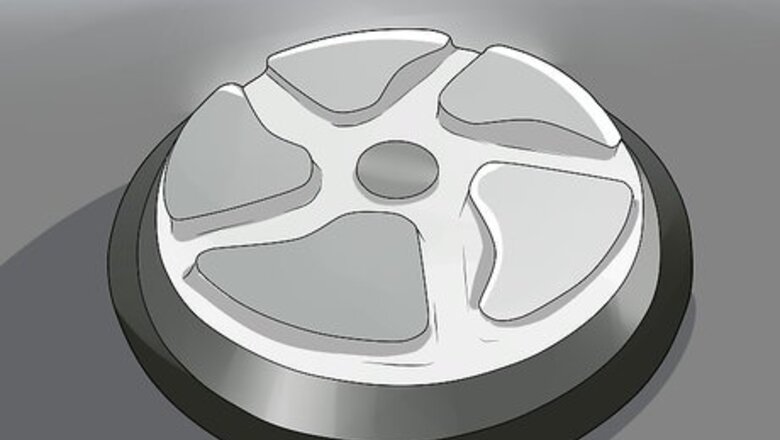
views
Creating a Good Surface
Find an appropriate mold. Before you can start making something from carbon fiber, you need to have a mold. The mold shapes the carbon fiber into the form that you want. You can buy molds online, or at other retailers. Carbon fiber parts are popular in automobile and motorcycle industries, and you can often buy molds from suppliers. In some cases, you can use the original part as a mold to make the carbon fiber part. This will not work well if the part is damaged.
Wear the appropriate protective equipment when dealing with carbon fiber. At a minimum, you should wear protective gloves, goggles, and a face mask. This gear will help prevent the inhalation of potentially fatal fumes or the absorption of harmful solvents through the skin. In addition to the gear, work in an area that is relatively well ventilated to avoid excessive gas build up.
Prepare the mold. Before proceeding, the mold should be sprayed with a material that allows the part to separate from the mold once it is finished. These materials are usually a specialized type of wax that does not interfere with the curing process of the part. You can order a mold lubricant online or buy one from a carbon fiber retailer. The wax is not to be confused with the resin. The wax creates a layer between the mold and the resin, and does not harden.
Spray the inside with resin. For best results, make sure that all nooks and crannies of the mold are completely saturated with the resin. Depending on the size of the mold, you may need multiple cans of resin This will create the surface needed to apply the carbon fiber. Unlike the wax, the resin will harden and be removed from the mold as part of the carbon fiber piece.
Laying the Carbon Fiber
Apply the fiber cloth. Quickly press sheets of carbon fiber cloth into the mold. As with applying the resin, make sure you completely cover all sections of the interior mold with the fiber cloth. If there are particularly small corners or angles, you may want to consider pressing the fiber cloth into the crannies with a screwdriver or other small tool.
Add additional resin. Spray the inside of the mold with more resin. The fiber cloth should be completely saturated with the resin. This is what bonds the fibers of the cloth together and gives carbon fiber its strength.
Bag the mold. To avoid dirt and dust falling into the resin and to get the fiber cloth to conform better to the mold, you can bag the mold. This means placing a bag over the mold with a vacuum attachment. Then, use a vacuum pump (or for a crude version a vacuum cleaner) to pull suction on the bag. This will also help the resin dry faster.
Heat the carbon fiber. Heating the carbon fiber part will speed up the curing process. You should heat the part to between 250 °F (121 °C) and 350 °F (177 °C) for several hours. Alternatively, you can allow the part to cure more slowly without heat. This usually takes at least 24 hours. Most resins will not cure well below 60 °F (16 °C). You should not cure the part in a kitchen stove. The fumes given off smell terrible and they are toxic. You need an autoclave or other heat source for the curing process.
Finishing the Part
Apply at least three more layers of resin. These layers of resin are intended to improve the look of the part, not the strength or functionality. Allow each layer of resin to set up before putting on the next layer. This can take anywhere from a few minutes to hours, but you will be able to tell because the resin will get tacky (sticky) when it is ready for the next coat.
Sand the top layer of resin. Once you have applied three to seven layers of resin, it is time to sand it. You should sand out any imperfections in the resin, like dust particles or uneven surfaces. Take care not to go through the resin, if you sand the fibers underneath you will destroy the part.
Polish the part. After you have sanded the imperfections out of the resin, you can polish it. You can buy a polish appropriate for your resin at the same retailer that you purchased the resin. Apply the polish with a clean, soft rag, and wipe it off with another clean, soft rag. This will give the part a nice shine.
Inspect the carbon fiber part on all sides. Make sure that there are no cracks or other deformations on the part. If the part is damaged, you will have to start over and make another part. If you don’t see any imperfections, you can use the part.
Creating Carbon Fibers in a Factory
Dissolve the precursor. Precursor is the material that you use to make the carbon fiber. Almost all carbon fiber is made from a polyacrylonitrile precursor. You should dissolve the polyacrylonitrile in an organic solvent such as dimethyl sulfoxide.
Spin the polymer. Once the precursor is dissolved, you put it in a coagulation bath. Then, run the slush through a spinneret. The material is forced through the fine holes of the spinneret to create long strands.
Add oxygen. Oxygen is needed to crosslink the polymers and make them more suitable for fibers. To oxidize the strands, heat them in an oxidation oven that ranges from 200 °C (392 °F) to 300 °C (572 °F). You must maintain appropriate airflow during this process to avoid catching the strands on fire.
Pyrolyze the polymer chains. Once oxidized, the strands must be heated in an oxygen free environment. Since there is no oxygen, the strands will not burn. Instead, they undergo a process called pyrolysis, which removes almost all impurities, such as organic solvents. A series of pyrolysis ovens are used that range anywhere from 700 °C (1,292 °F) to 1,500 °C (2,730 °F).
Treat the fibers. Pyrolysis leaves you with carbon fiber threads. Before being shipped to customers or processing plants, the threads must be treated. This includes etching the fibers with an acid, such as nitric acid. After etching (referred to as treatment) the fiber is coated in a process called sizing. The coating increases the size of the fibers and makes them more sturdy for processing and customer use.
Comments
0 comment